Aircraft Specialty Clamp Market Projected to Reach $1.25 Billion by 2025: Key Insights from the U.S., Germany, and Japan
Aircraft Specialty Clamp Market insights reveal strong growth driven by rising aerospace industry demand, especially in the U.S., Germany, and Japan. Featuring precision-engineered clamps for manufacturing and maintenance, the market is shaped by advanced materials, 3D printing, and smart technologies. Challenges include stringent certification and geopolitical trade impacts. Explore trends, applications, regional analysis, and future outlook to understand this $1.25 billion market projected by 2025.
- Last Updated:
Aircraft Specialty Clamp Market Sees Steady Momentum in Q1 and Q2 2025
The Aircraft Specialty Clamp market is projected to reach $1.25 billion in 2025, advancing at a CAGR of 5.7% through 2033. During Q1 2025, the market reached approximately $310 million, with Q2 following closely at around $317 million, supported by stable aircraft production volumes and increased retrofitting activities in commercial and defense aviation.
In the U.S., rising investments in defense aviation and MRO (maintenance, repair, and overhaul) services boosted demand for high-precision clamps. Germany observed strong performance in Q2, particularly due to its established aerospace manufacturing base, while Japan experienced gradual growth through enhanced integration of lightweight and vibration-resistant clamp solutions in regional aircraft models.
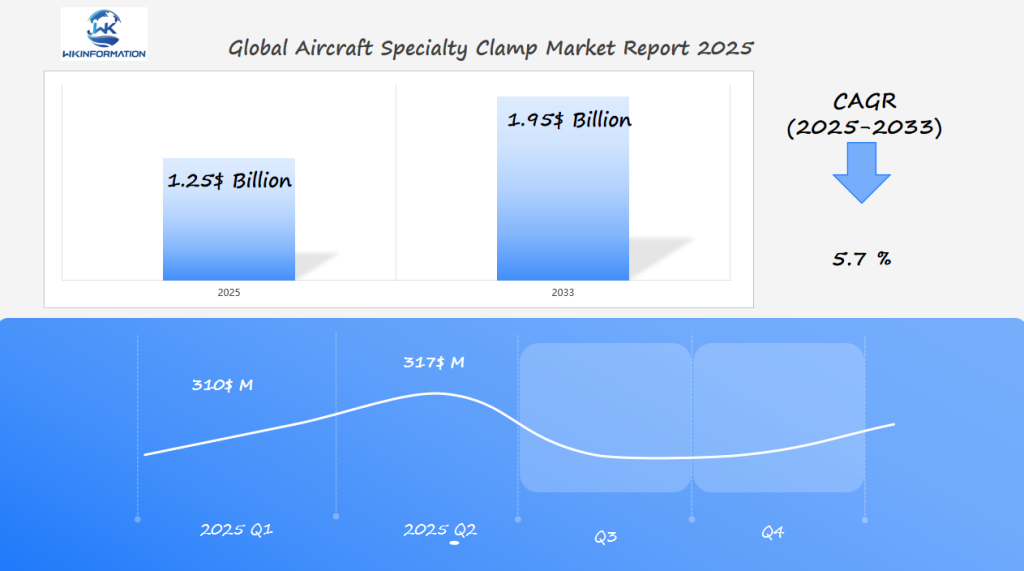
Key Takeaways
- The Aircraft Specialty Clamp Market is projected to reach $1.25 billion by 2025.
- Growing demand from the aerospace industry is a key driver.
- Precision-engineered clamps are increasingly critical in aircraft manufacturing.
- Market growth is supported by
- advancements in aerospace applications
- The U.S. is a significant contributor to the market’s expansion.
Aircraft Specialty Clamp Market Upstream and Downstream Industry Chain Analysis
Understanding the aircraft specialty clamp market requires a deep dive into its industry chain analysis, covering both upstream and downstream sectors. The upstream industry plays a critical role in providing the necessary raw materials and components, while the downstream industry is responsible for the distribution and application of these clamps.
Upstream Industry Analysis
The upstream industry for aircraft specialty clamps involves several key components, including raw material suppliers, manufacturers of clamp components, and other supporting industries. The quality and availability of raw materials, such as metals and alloys, significantly impact the production of specialty clamps.
Raw Material Suppliers
Raw material suppliers are crucial in the production of aircraft specialty clamps. They provide essential materials like titanium, stainless steel, and other high-strength alloys that are used in clamp manufacturing. The reliability and quality of these suppliers directly affect the final product’s performance and durability.
Raw Material Application Key Characteristics Titanium | High-strength clamp components | High strength-to-weight ratio, corrosion resistance |
Stainless Steel | Clamp body and fasteners | Corrosion resistance, durability |
High-Strength Alloys | Specialized clamp applications | High tensile strength, resistance to extreme temperatures |
The table above highlights the critical raw materials used in the production of aircraft specialty clamps, their applications, and key characteristics. Ensuring the quality of these materials is paramount for the overall performance of the clamps.
Trends in Aircraft Specialty Clamps for Aerospace Applications in 2025
As we approach 2025, new trends in aircraft specialty clamps are changing the aerospace industry. The need for clamps that are more efficient, dependable, and lightweight is pushing for new ideas and advancements in this field.
Emerging Trends
The aerospace industry is witnessing several emerging trends in aircraft specialty clamps. These include the development of clamps with advanced materials and designs that offer higher strength-to-weight ratios.
A key trend is the increasing use of advanced composites in clamp manufacturing. These materials provide significant advantages in terms of weight reduction and durability.
Technological Advancements
Technological advancements are playing a crucial role in the evolution of aircraft specialty clamps. Some of the significant advancements include:
- 3D printing technology for complex clamp designs
- Advanced coating technologies for improved corrosion resistance
- Integration of smart technologies for real-time monitoring
The integration of smart technologies into aircraft specialty clamps is an emerging trend that is expected to gain traction by 2025. This involves the use of sensors and IoT devices to monitor clamp performance and predict potential failures.
These trends and technological advancements are set to revolutionize the aircraft specialty clamp market, enabling more efficient and reliable aerospace applications.
Challenges in the Manufacturing and Certification of Aircraft Specialty Clamps
The manufacturing and certification of aircraft specialty clamps pose significant challenges that impact the aerospace industry. These components, such as the ones shown in the images below, are crucial for aircraft safety and performance, necessitating high standards in their production and certification.
Manufacturing Challenges
The production of aircraft specialty clamps involves complex processes that require precision and high-quality materials. Manufacturing challenges include maintaining consistency in production, adhering to stringent quality control measures, and utilizing advanced technologies to meet the required specifications.
One of the significant manufacturing challenges is ensuring the durability and reliability of the clamps under various environmental conditions. This requires rigorous testing and inspection protocols to guarantee that the clamps can withstand the stresses of flight operations.
Certification Processes
Obtaining certification for aircraft specialty clamps is a rigorous process that involves compliance with industry standards and regulatory requirements. Certification processes are critical to ensuring that these components meet the necessary safety and performance standards.
The certification process typically involves several stages, including design validation, material inspection, and performance testing. Manufacturers must provide detailed documentation to demonstrate compliance with relevant standards, such as those set by the Federal Aviation Administration (FAA) or other aviation authorities.
- Compliance with industry standards
- Rigorous testing and inspection
- Detailed documentation and record-keeping
Ensuring quality control throughout the manufacturing and certification processes is essential. This involves implementing robust quality management systems that can track and verify every stage of production and testing.
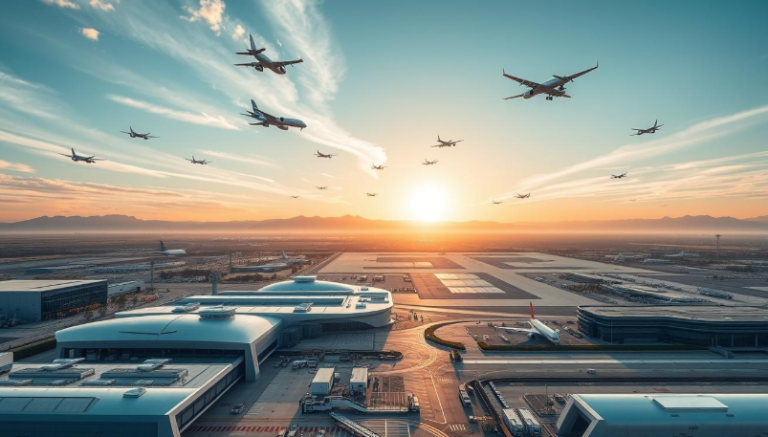
Geopolitical Impact on Aircraft Specialty Clamp Production and International Trade
Geopolitical dynamics are important in shaping the Aircraft Specialty Clamp industry, affecting both production and global trade. The complex network of international relations, trade agreements, and regulatory policies directly influences the supply chain and operational viability of manufacturers in this sector.
Geopolitical Factors
The Aircraft Specialty Clamp market is affected by many geopolitical factors, including trade tensions, sanctions, and export controls. These factors can disrupt the flow of critical components and materials, leading to production delays and increased costs for manufacturers.
Impact of Trade Policies
- Tariffs imposed on imported goods can make it more expensive for manufacturers to source raw materials or components from foreign suppliers.
- Trade agreements between countries can influence the cost and availability of raw materials.
Understanding and navigating the complex landscape of trade policies and regulations is crucial for companies operating in the global Aircraft Specialty Clamp market. Compliance with these regulations is not only mandatory but also critical for maintaining a competitive edge in the international market.
Consequences of Export Controls and Sanctions
- Export controls can limit market access for manufacturers.
- Sanctions can affect the ability of companies to conduct business with certain countries or entities.
By closely monitoring geopolitical developments and adapting to changes in trade policies and regulations, companies in the Aircraft Specialty Clamp industry can mitigate risks and capitalize on emerging opportunities in the global market.
Importance of Regulatory Compliance
Regulatory compliance is essential for avoiding legal and financial repercussions. Companies must stay informed about applicable laws and regulations in the countries they operate in to ensure they are meeting their obligations.
Type Segmentation: Custom vs. Standard Aircraft Specialty Clamps
Understanding the differences between custom and standard aircraft specialty clamps is crucial for industry stakeholders.
The aircraft specialty clamp market has a wide variety of products, mainly divided into two categories: custom clamps and standard clamps. Custom clamps are made for specific uses, providing customized solutions for one-of-a-kind needs. These clamps are designed to meet exact specifications, making them essential in intricate aerospace applications.
Design and Application of Custom Aircraft Specialty Clamps
Custom aircraft specialty clamps are made to meet specific needs that standard clamps cannot satisfy. They are designed with great care to ensure they meet the strict standards of modern aircraft manufacturing and maintenance.
Characteristics of Standard Aircraft Specialty Clamps
On the other hand, standard clamps offer a cost-effective solution for common applications. These clamps are manufactured according to established specifications and are widely used in various aerospace applications where their characteristics are well-suited.
Standard clamps have several advantages, including:
- Easy to procure
- Lower costs compared to custom clamps
- Widely available
A comparison between custom and standard clamps is provided in the following table:
Characteristics Custom Clamps Standard Clamps Design Specificity | Tailored to specific applications | General-purpose design |
Cost | Generally more expensive | Cost-effective |
Availability | Typically made to order | Widely available |
The choice between custom and standard aircraft specialty clamps depends on the specific requirements of the application. While custom clamps offer tailored solutions, standard clamps provide a cost-effective alternative for common needs.
Applications of Aircraft Specialty Clamps in Aircraft Manufacturing and Maintenance
In the world of aircraft production and maintenance, Aircraft Specialty Clamps are essential. Their flexibility and accuracy make them crucial in both manufacturing and maintenance activities.
Aircraft Manufacturing
Aircraft Specialty Clamps are crucial in the assembly of aircraft components. They ensure that parts are held securely in place, allowing for precise alignment and joining. This precision is critical in aircraft manufacturing, where even minor deviations can have significant safety implications.
The use of these clamps in manufacturing also streamlines production processes. By providing a reliable means of securing components, they reduce the time and labor required for assembly. This efficiency is essential in meeting the demanding production schedules of the aerospace industry.
Aircraft Specialty Clamps in Manufacturing
Application Area Role of Aircraft Specialty Clamps Benefits Aircraft Manufacturing | Secure assembly of components | Precision, Efficiency |
Maintenance, Repair, and Overhaul (MRO)
In the context of Maintenance, Repair, and Overhaul (MRO), Aircraft Specialty Clamps facilitate the efficient repair and replacement of aircraft parts. Their design allows for easy access to complex areas of the aircraft, reducing downtime and enhancing overall maintenance efficiency.
The role of these clamps in MRO is multifaceted. They not only support the structural integrity of the aircraft during maintenance but also enable technicians to perform repairs with greater precision and speed.
Role of Aircraft Specialty Clamps in MRO
Application Area Role of Aircraft Specialty Clamps Benefits MRO | Facilitate repair and replacement | Reduced Downtime, Enhanced Efficiency |
The importance of Aircraft Specialty Clamps in both manufacturing and MRO underscores their value to the aerospace industry. As the demand for air travel continues to grow, the need for efficient, reliable aircraft manufacturing and maintenance processes will only increase, further highlighting the critical role of these clamps.
Global Market Overview: Regional Growth and Demand for Aircraft Specialty Clamps
The global market for aircraft specialty clamps is influenced by various regional trends and factors driving demand. It is important for manufacturers and suppliers to understand these regional dynamics in order to find opportunities and overcome challenges.
Regional Market Analysis
Regional differences in the aircraft specialty clamp market are influenced by factors such as aerospace industry growth, regulatory environments, and economic conditions. For example, regions with a strong aerospace industry presence tend to have a higher demand for specialty clamps.
The demand drivers for aircraft specialty clamps vary across regions. In some areas, the growth of the aerospace industry is a significant driver, while in others, it is the need for maintenance and repair that fuels demand.
Growth Drivers and Challenges
Key growth drivers for the regional aircraft specialty clamp market include:
- Increasing aerospace industry production
- Rising demand for commercial aircraft
- Growing need for maintenance, repair, and overhaul (MRO) services
However, there are also challenges to be addressed, such as:
- Stringent regulatory requirements
- Fluctuations in raw material prices
- Competition from alternative fastening solutions
By understanding these regional growth drivers and challenges, manufacturers and suppliers can better navigate the complex global market for aircraft specialty clamps.
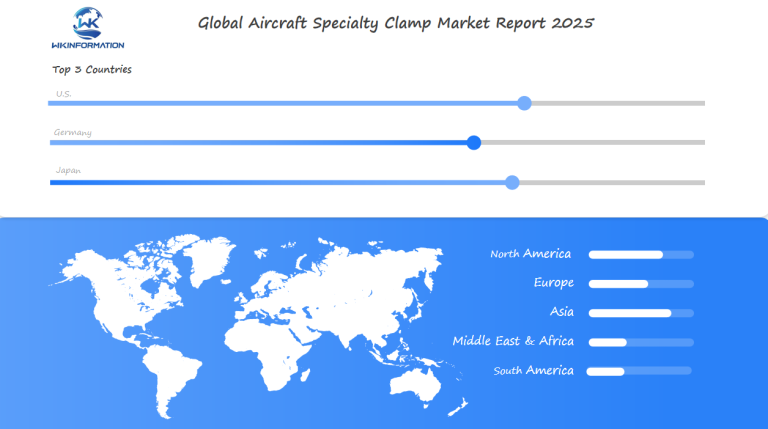
U.S. Market Insights: Strong Aerospace Sector Driving Aircraft Specialty Clamp Demand
The U.S. aerospace sector, known for its advanced manufacturing capabilities, is significantly contributing to the growth of the aircraft specialty clamp market. The presence of major aircraft manufacturers and a robust maintenance, repair, and overhaul (MRO) sector in the country is driving the demand for these specialized components.
U.S. Aerospace Industry Overview
The U.S. aerospace industry is a significant contributor to the country’s economy, with a strong presence of leading aircraft manufacturers such as Boeing and Lockheed Martin. The industry’s demand for high-quality, precision-engineered components like aircraft specialty clamps is consistently high.
The MRO sector in the U.S. also plays a crucial role in driving the demand for these clamps, as regular maintenance and repair activities require a steady supply of such components.
Demand Drivers in the U.S. Market
Several factors are driving the demand for aircraft specialty clamps in the U.S. market:
- Increased aircraft production rates
- Growing demand for commercial aircraft
- Expansion of the MRO sector
- Advancements in aerospace technology
These demand drivers are expected to continue influencing the market positively, with the U.S. remaining a key region for aircraft specialty clamp manufacturers.
Demand Driver | Impact on Market |
Increased Aircraft Production | Higher demand for specialty clamps |
Growing Commercial Aircraft Demand | Increased need for precision components |
MRO Sector Expansion | Steady supply required for maintenance |
Technological Advancements | Opportunities for innovative clamp solutions |
Germany’s High-Precision Aircraft Manufacturing and Need for Specialty Clamps
Germany’s reputation for high-precision manufacturing in the aerospace sector creates a significant need for advanced specialty clamps. The country’s aerospace industry is characterized by a strong focus on quality and precision, driving the demand for sophisticated clamping solutions.
Germany’s Aerospace Industry
The German aerospace industry is a critical component of the country’s industrial base, with a strong emphasis on innovation and precision engineering. High-precision manufacturing is a hallmark of this industry, with companies investing heavily in advanced technologies and processes.
Germany’s aerospace sector is known for its rigorous quality standards, which necessitates the use of high-quality specialty clamps in aircraft manufacturing. These clamps are essential for ensuring the precise assembly and maintenance of aircraft components.
Precision Manufacturing Requirements
The precision manufacturing requirements in Germany’s aerospace industry are stringent, with a focus on achieving exacting tolerances and specifications. Specialty clamps play a crucial role in meeting these requirements, providing the necessary precision and reliability.
The following table highlights the key precision manufacturing requirements in Germany’s aerospace industry and the role of specialty clamps:
Requirement | Description | Role of Specialty Clamps |
High Precision | Achieving exacting tolerances and specifications | Providing precise clamping solutions |
Quality Standards | Rigorous quality control and assurance | Ensuring reliable and consistent clamping performance |
Advanced Materials | Working with advanced materials and composites | Designing clamps compatible with various materials |
Germany’s Aerospace Industry
The demand for specialty clamps in Germany’s aerospace industry is driven by the need for high-precision manufacturing and the importance of maintaining stringent quality standards. As the industry continues to evolve, the role of specialty clamps will remain critical in ensuring the precision and reliability of aircraft manufacturing and maintenance.
Japan’s Aerospace Industry and the Growing Demand for Aircraft Specialty Clamps
Japan’s aerospace industry is experiencing significant growth due to technological advancements and strategic government initiatives. This expansion is not only reshaping the country’s aerospace sector but also increasing the demand for specialized parts, such as aircraft specialty clamps.
Japan’s Aerospace Sector Overview
Japan’s aerospace industry has been steadily evolving, with significant investments in research and development, as well as collaborations with international partners. The industry’s growth is driven by the government’s proactive policies and the increasing demand for advanced aerospace technologies.
Key players in Japan’s aerospace sector include Mitsubishi Heavy Industries, Kawasaki Heavy Industries, and Japan Aerospace Exploration Agency (JAXA), which are playing crucial roles in shaping the industry’s future.
The growing demand for aircraft specialty clamps in Japan’s aerospace industry presents emerging opportunities for manufacturers and suppliers. As the industry continues to expand, there is a need for high-quality, precision-engineered clamps that meet stringent aerospace standards.
- Increased demand for commercial aircraft
- Advancements in aerospace technologies
- Government initiatives supporting the aerospace industry
By capitalizing on these emerging opportunities, companies can establish themselves as key players in Japan’s aerospace sector and benefit from the industry’s growth.
Future Outlook: Technological Advancements in Aircraft Specialty Clamps
The aircraft specialty clamp market is on the verge of a technological revolution, driven by advancements in materials and design. This transformation is expected to enhance the performance, reliability, and safety of aircraft specialty clamps.
As the aerospace industry continues to evolve, the demand for more sophisticated clamps is rising. Emerging technologies such as 3D printing and advanced materials are playing a crucial role in this development.
Emerging Technologies
The integration of emerging technologies is set to revolutionize the production and functionality of aircraft specialty clamps. Some of the key technologies include:
- Advanced materials that offer higher strength-to-weight ratios
- 3D printing for complex clamp designs
- Smart technologies for real-time monitoring
Advanced materials, such as high-strength alloys and composites, are being increasingly used to manufacture clamps that can withstand extreme conditions.
Future Developments
The future of aircraft specialty clamps will be shaped by ongoing research and development in several key areas. Some of the anticipated developments include:
Technology Application Benefits 3D Printing | Complex clamp designs | Enhanced precision, reduced weight |
Advanced Materials | High-strength, lightweight clamps | Improved durability, reduced fuel consumption |
Smart Technologies | Real-time monitoring and diagnostics | Enhanced safety, predictive maintenance |
As these technologies continue to evolve, they are expected to drive significant improvements in the aircraft specialty clamp market, enabling the production of more efficient, reliable, and safe clamps.
Competitive Landscape: Leading Players in the Aircraft Specialty Clamp Market
The aircraft specialty clamp market is highly competitive, with several key players driving innovation and growth through advanced manufacturing techniques and strategic partnerships. These leading companies focus on leveraging emerging technologies such as 3D printing, advanced materials, and smart monitoring systems to enhance product performance and meet stringent aerospace standards.
Key Players
- Applied Aerospace Structures Corporation (AASC) – United States
- SMS (Specialty Manufacturing Solutions) – United States
- Gordian Strapping Inc. – United States
- Karman Rubber Company – United States
- Airtec Systems Inc. – United States
- Flexco – United States
- Fastex International – United States
- LISI Aerospace – France
- Voss Aerospace – United States
- Aviation Spares & Equipment Ltd. (ASE) – United Kingdom
Overall
Report Metric | Details |
---|---|
Report Name | Global Aircraft Specialty Clamp Market Report |
Base Year | 2024 |
Segment by Type | ·Custom
·Standard |
Segment by Application | ·Aircraft Manufacturing
·Maintenance, Repair, and Overhaul (MRO) |
Geographies Covered | ·North America (United States, Canada)
·Europe (Germany, France, UK, Italy, Russia) ·Asia-Pacific (China, Japan, South Korea, Taiwan) ·Southeast Asia (India) ·Latin America (Mexico, Brazil) |
Forecast units | USD million in value |
Report coverage | Revenue and volume forecast, company share, competitive landscape, growth factors and trends |
The Aircraft Specialty Clamp Market is growing due to the rising need for top-notch, precision-engineered clamps in the aerospace industry. As mentioned earlier, several factors such as geopolitical events, technological advancements, and regional demand impact the market.
A comprehensive understanding of the market dynamics, trends, and challenges is crucial for stakeholders to navigate this complex landscape. The market summary highlights the key areas of focus, including type segmentation, applications, and regional growth.
As the market continues to evolve, staying informed about the latest developments will be essential for success. With the U.S., Germany, and Japan being key players in the aerospace industry, their demand for aircraft specialty clamps is expected to drive market growth. The Aircraft Specialty Clamp Market is poised for significant growth, and a thorough market summary will help stakeholders make informed decisions.
Global Aircraft Specialty Clamp Market Report (Can Read by Free sample) – Table of Contents
Chapter 1: Aircraft Specialty Clamp Market Analysis Overview
- Competitive Forces Analysis (Porter’s Five Forces)
- Strategic Growth Assessment (Ansoff Matrix)
- Industry Value Chain Insights
- Regional Trends and Key Market Drivers
- Aircraft Specialty Clamp Market Segmentation Overview
Chapter 2: Competitive Landscape
- Global Aircraft Specialty Clamp Players and Regional Insights
-
- Key Players and Market Share Analysis
- Sales Trends of Leading Companies
- Year-on-Year Performance Insights
- Competitive Strategies and Market Positioning
-
- Key Differentiators and Strategic Moves
Chapter 3: Aircraft Specialty Clamp Market Segmentation Analysis
- Key Data and Visual Insights
-
- Trends, Growth Rates, and Drivers
- Segment Dynamics and Insights
-
- Detailed Market Analysis by Segment
Chapter 4: Regional Market Performance
- Consumer Trends by Region
-
- Historical Data and Growth Forecasts
- Regional Growth Factors
-
- Economic, Demographic, and Technological Impacts
- Challenges and Opportunities in Key Regions
- Regional Trends and Market Shifts
- Key Cities and High-Demand Areas
Chapter 5: Aircraft Specialty Clamp Emerging and Untapped Markets
- Growth Potential in Secondary Regions
-
- Trends, Challenges, and Opportunities
Chapter 6: Product and Application Segmentation
- Product Types and Innovation Trends
- Application-Based Market Insights
Chapter 7: Aircraft Specialty Clamp Consumer Insights
- Demographics and Buying Behaviors
-
- Target Audience Profiles
Chapter 8: Key Findings and Recommendations
- Summary of Aircraft Specialty Clamp Market Insights
Actionable Recommendations for Stakeholders
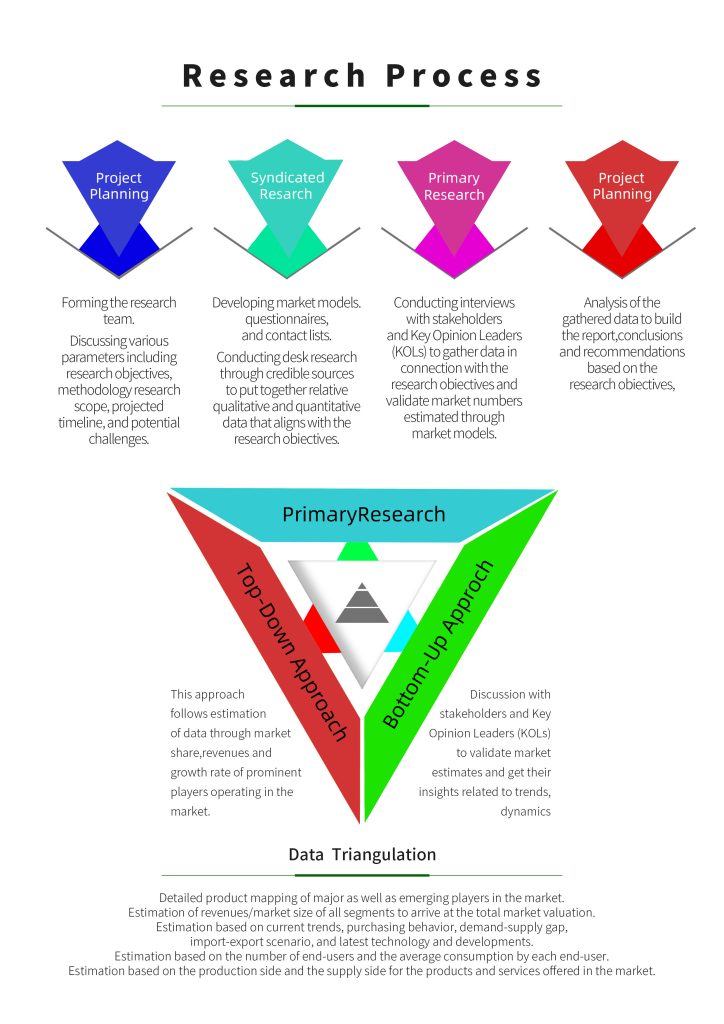
Access the study in MULTIPLEFORMATS
Didn’t find what you’re looking for?
TALK TO OUR ANALYST TEAM
Need something within your budget?
NO WORRIES! WE GOT YOU COVERED!
Call us on: +1-866-739-3133
Email: infor@wkinformation.com
What is driving the growth of the Aircraft Specialty Clamp Market?
The growth of the Aircraft Specialty Clamp Market is driven by increasing demand from the aerospace industry, particularly in the U.S., due to the rising need for specialized clamps in aircraft manufacturing and maintenance.
What are the key trends in Aircraft Specialty Clamps for aerospace applications?
Emerging trends include technological advancements, such as the development of lightweight and high-strength materials, driving innovation in clamp design.
What are the challenges in the manufacturing and certification of Aircraft Specialty Clamps?
Manufacturers face challenges in ensuring the quality and reliability of Aircraft Specialty Clamps, adhering to stringent certification processes, and meeting regulatory requirements.
How do geopolitical factors impact the Aircraft Specialty Clamp Market?
Geopolitical factors, including trade policies, regulations, and geopolitical tensions, can affect the supply chain, impacting manufacturers and consumers alike.
What is the difference between custom and standard Aircraft Specialty Clamps?
Custom clamps are designed for specific applications, offering tailored solutions, while standard clamps provide a cost-effective solution for common applications.
What are the applications of Aircraft Specialty Clamps in aircraft manufacturing and maintenance?
Aircraft Specialty Clamps are essential in both aircraft manufacturing and maintenance. They ensure accurate assembly during production and make repairs and part replacements more efficient during maintenance.
Which regions are driving the demand for Aircraft Specialty Clamps?
The demand for Aircraft Specialty Clamps varies by region, with the U.S., Germany, and Japan being significant markets due to their strong aerospace industries.
What is the future outlook for the Aircraft Specialty Clamp Market?
The future of the Aircraft Specialty Clamp Market is shaped by technological advancements, emerging trends, and innovations, such as advanced materials and smart technologies.
What is the impact of raw material suppliers on the Aircraft Specialty Clamp Market?
Raw material suppliers play a critical role in ensuring the consistency and quality of Aircraft Specialty Clamps, as the quality and availability of raw materials significantly impact production.
How does the U.S. aerospace industry influence the demand for Aircraft Specialty Clamps?
The U.S. aerospace industry drives the demand for Aircraft Specialty Clamps due to the presence of major aircraft manufacturers and a strong MRO sector.