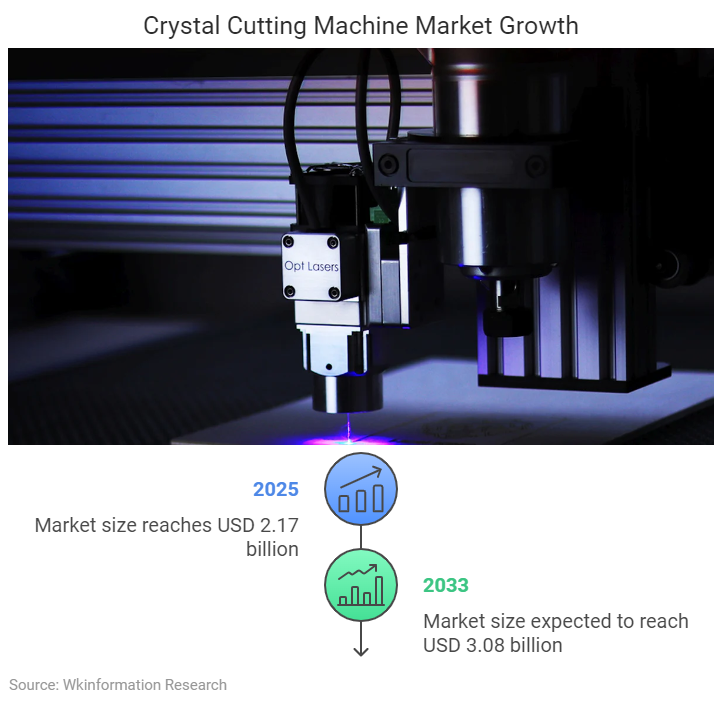
The crystal cutting machine market is undergoing a transformative phase, driven by advancements in technology and shifting industry demands. Transitioning from traditional methods, manufacturers now employ cutting-edge techniques like diamond wire and laser cutting. These innovations enhance precision, reduce material waste, and improve efficiency. Automation and material handling capabilities further streamline operations, addressing the growing need for accuracy in electronics, optics, and jewelry production. The market size will reach USD 2.17 billion in 2025 and is expected to reach USD 3.08 billion by 2033, with a CAGR of 4.47% from 2025 to 2033. As these trends shape the market, stakeholders must adapt to remain competitive in this rapidly evolving landscape.
Key Insights
- New tech like AI and lasers improve accuracy and speed in cutting.
- The semiconductor and jewelry fields boost demand for better cutting tools.
- Being eco-friendly matters; companies use energy-saving machines and cut waste.
- Growing markets in Latin America and the Middle East offer chances to expand.
- Training workers is key to solving the lack of skilled machine operators.
Key Market Trends in 2025
Growth Drivers
Rising demand for precision in electronics and optics
The increasing need for precision in electronics and optics is a significant driver of the crystal cutting machine market. Industries like semiconductor manufacturing and optoelectronics rely heavily on advanced cutting technologies to meet stringent quality standards. For instance, the production of LED components requires precise cutting of sapphire substrates to minimize defects and enhance light performance. This demand underscores the importance of adopting cutting-edge technology trends to achieve higher accuracy and efficiency.
Expansion of the semiconductor and jewelry industries
The semiconductor and jewelry industries are experiencing rapid growth, further fueling the demand for crystal cutting machines. Semiconductor manufacturing, essential for producing chips and electronic components, has seen a surge in global demand. Similarly, the jewelry sector requires high-precision cutting for gemstones, driving innovation in cutting techniques. These industries highlight the critical role of manufacturing advancements in meeting market needs.
Challenges Facing the Market
High initial investment costs
The high initial investment costs associated with crystal cutting machines remain a significant challenge. Advanced machines, such as diamond wire saws for silicon crystal slicing, require substantial capital. This financial barrier limits adoption, particularly among small and medium-sized enterprises.
Limited availability of skilled operators
Operating these technologically advanced machines demands specialized skills. However, the limited availability of skilled operators poses a challenge for manufacturers. Training programs and workforce development initiatives are essential to address this issue and ensure the efficient use of cutting-edge technology.
Regional Market Dynamics
Growth in Asia-Pacific due to manufacturing hubs
The Asia-Pacific region is the fastest-growing market for crystal cutting machines. Several factors contribute to this growth:
- The electronics sector drives demand for silicon wafers.
- The region’s strong manufacturing capabilities attract vendors.
- The increasing need for advanced manufacturing technologies supports market expansion.
North America and Europe focusing on innovation and R&D
North America and Europe prioritize innovation and research and development (R&D) to maintain their competitive edge. These regions invest heavily in developing advanced cutting techniques and sustainable manufacturing practices, aligning with global technology trends.
Emerging markets in Latin America and the Middle East
Emerging markets in Latin America and the Middle East present new opportunities for growth. These regions are gradually adopting advanced manufacturing technologies, driven by increasing industrialization and demand for high-quality products.
Technological Advancements in Crystal Cutting Machines
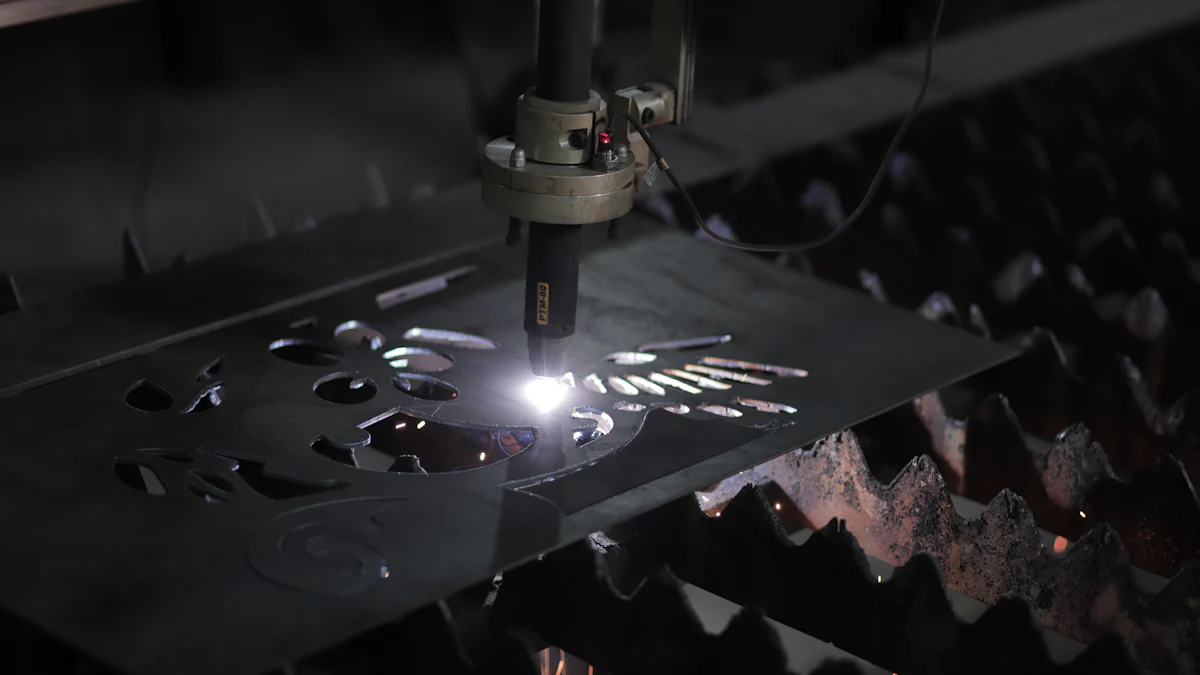
AI and Machine Learning Integration
Enhancing precision and reducing errors
Artificial intelligence (AI) and machine learning are revolutionizing the crystal cutting machine industry. These technologies enable machines to analyze vast datasets, improving cutting precision and minimizing errors. For example, AI algorithms can detect patterns in material properties, allowing machines to adjust cutting parameters in real time. This capability ensures consistent quality, even in complex manufacturing processes. As a result, manufacturers can meet stringent industry standards while reducing material waste.
Predictive maintenance for improved efficiency
Machine learning also plays a critical role in predictive maintenance. By analyzing operational data, these systems can identify potential issues before they lead to machine downtime. This proactive approach enhances efficiency and reduces maintenance costs. Manufacturers benefit from uninterrupted production cycles, which supports growth in industries like electronics and jewelry.
Automation and Robotics
Streamlining production processes
Automation is transforming manufacturing processes in the crystal cutting machine industry. Companies like Crystal International are leveraging digital technologies to optimize operations.
- They have re-engineered their manufacturing workflows to integrate automation at every stage.
- Advanced technologies streamline processes such as cutting, sewing, and finishing.
- These efforts aim to achieve manufacturing excellence by improving product quality and efficiency.
Reducing labor dependency
Robotics further reduces dependency on manual labor. Automated systems handle repetitive tasks with precision, freeing human operators to focus on more complex responsibilities. This shift not only enhances productivity but also addresses the challenge of limited skilled labor availability. Additionally, automation reduces environmental impact by optimizing resource usage.
Innovations in Cutting Techniques
Laser cutting for higher accuracy
Laser cutting has emerged as a leading technology trend in crystal cutting. This technique offers unparalleled accuracy, making it ideal for applications requiring intricate designs. It eliminates the need for post-processing, saving time and resources. Furthermore, laser cutting minimizes tool wear, extending the lifespan of equipment and reducing operational costs.
Ultrasonic cutting for delicate materials
Ultrasonic cutting is another significant innovation in the industry. This method is particularly effective for brittle materials, as it generates negligible heat during the cutting process. The table below highlights its benefits:
Benefit | Description |
---|---|
Can Process Hard Materials | Ultrasonic cutting is effective for brittle materials. |
Negligible Heat Generation | This technique minimizes heat impact on materials. |
Minimal Tool Wear | Reduces wear on tools, extending their lifespan. |
No Post-Processing Required | Eliminates the need for additional finishing steps. |
These cutting-edge techniques demonstrate how innovation continues to drive growth and efficiency in the crystal cutting machine market.
Impact of Quantum Computing
Enabling complex simulations for cutting processes
Quantum computing is revolutionizing the crystal cutting machine industry by enabling highly complex simulations. Traditional computing systems often struggle to process the intricate calculations required for advanced cutting processes. Quantum systems, however, excel at handling these challenges. They allow manufacturers to simulate material properties and cutting dynamics with unprecedented accuracy. For example, quantum algorithms can predict how different materials will react to specific cutting techniques. This capability helps manufacturers optimize their processes before actual production begins, reducing trial-and-error approaches.
Additionally, quantum computing supports the development of new cutting methods. By simulating atomic-level interactions, it enables researchers to explore innovative techniques that were previously unattainable. These advancements not only improve precision but also enhance the overall efficiency of manufacturing operations. As a result, industries such as electronics and jewelry benefit from higher-quality outputs and reduced material waste.
Optimizing machine performance and design
Quantum computing also plays a pivotal role in optimizing the performance and design of crystal cutting machines. By analyzing vast datasets, quantum systems identify patterns and inefficiencies that traditional methods might overlook. This insight allows manufacturers to refine machine components and improve operational workflows. For instance, quantum models can suggest design modifications that enhance cutting speed without compromising accuracy.
Moreover, quantum computing facilitates real-time adjustments during the manufacturing process. Machines equipped with quantum-driven algorithms can adapt to changing conditions, ensuring consistent performance. This adaptability is particularly valuable in high-precision industries where even minor deviations can lead to significant losses. By leveraging quantum technology, manufacturers achieve greater reliability and scalability in their operations.
The integration of quantum computing marks a significant leap forward for the crystal cutting machine industry. It empowers manufacturers to push the boundaries of innovation while maintaining efficiency and precision.
Market Segmentation by Type and Application
By Type
Manual crystal cutting machines
Manual crystal cutting machines cater to industries requiring basic cutting operations. These machines rely on operator expertise, making them suitable for small-scale manufacturing. They are often used in workshops where precision is less critical, and production volumes are low. Despite their simplicity, they remain relevant due to their affordability and ease of use.
Semi-automatic crystal cutting machines
Semi-automatic machines combine manual control with automated features. These machines enhance efficiency while maintaining a degree of operator involvement. Industries such as jewelry and optics benefit from their ability to balance precision and cost-effectiveness. Their versatility makes them a popular choice for mid-sized manufacturing operations.
Fully automated crystal cutting machines
Fully automated machines represent the pinnacle of manufacturing technology in this sector. These machines operate with minimal human intervention, delivering unmatched precision and consistency. They are widely adopted in high-demand industries like electronics and semiconductors. Their advanced features, such as AI integration and robotics, streamline production processes and reduce material waste.
By Application
Electronics and semiconductors
The electronics and semiconductor industries drive significant demand for crystal cutting machines. These machines play a crucial role in producing silicon wafers, LED components, and other electronic materials. The table below highlights key applications:
Application | Description |
---|---|
Semiconductor Manufacturing | Essential for producing chips and electronic components, with a rise in global semiconductor demand. |
Solar Panel Production | Requires high-quality silicon wafers for photovoltaic cells, ensuring optimal efficiency. |
LED and Optoelectronics | Precision cutting of sapphire substrates for LEDs, minimizing defects for optimal light performance. |
Research & Development | Used for producing precise samples in materials science and photonics research. |
Jewelry and gemstones
The jewelry industry relies on crystal cutting machines for shaping and polishing gemstones. These machines ensure high precision, enhancing the aesthetic appeal of finished products. Advanced cutting techniques, such as laser and ultrasonic methods, enable intricate designs and reduce material loss.
Medical devices and optics
In the medical and optics sectors, crystal cutting machines are indispensable for producing components like lenses and surgical tools. These industries demand exceptional precision, which advanced cutting technologies can deliver. The machines also support innovation in optical instruments and medical device manufacturing.
By Region
Asia-Pacific
Asia-Pacific dominates the crystal cutting machine market due to its robust manufacturing hubs. Countries like China, Japan, and South Korea lead in electronics and semiconductor production. The region’s cost-effective labor and advanced manufacturing technology contribute to its rapid growth.
North America
North America emphasizes innovation and research in crystal cutting machines. The region invests heavily in developing sustainable manufacturing practices and cutting-edge technologies. Its focus on high-quality production supports industries like aerospace, electronics, and medical devices.
Europe
Europe prioritizes precision and sustainability in manufacturing. The region’s strong regulatory framework drives the adoption of eco-friendly practices. Germany and Switzerland, known for their engineering expertise, lead in developing advanced crystal cutting machines.
Latin America and the Middle East
Emerging markets in Latin America and the Middle East show increasing adoption of crystal cutting machines. Industrialization and growing demand for high-quality products drive market expansion in these regions. Governments also support manufacturing growth through favorable policies and investments.
Sustainability and Eco-Friendly Innovations
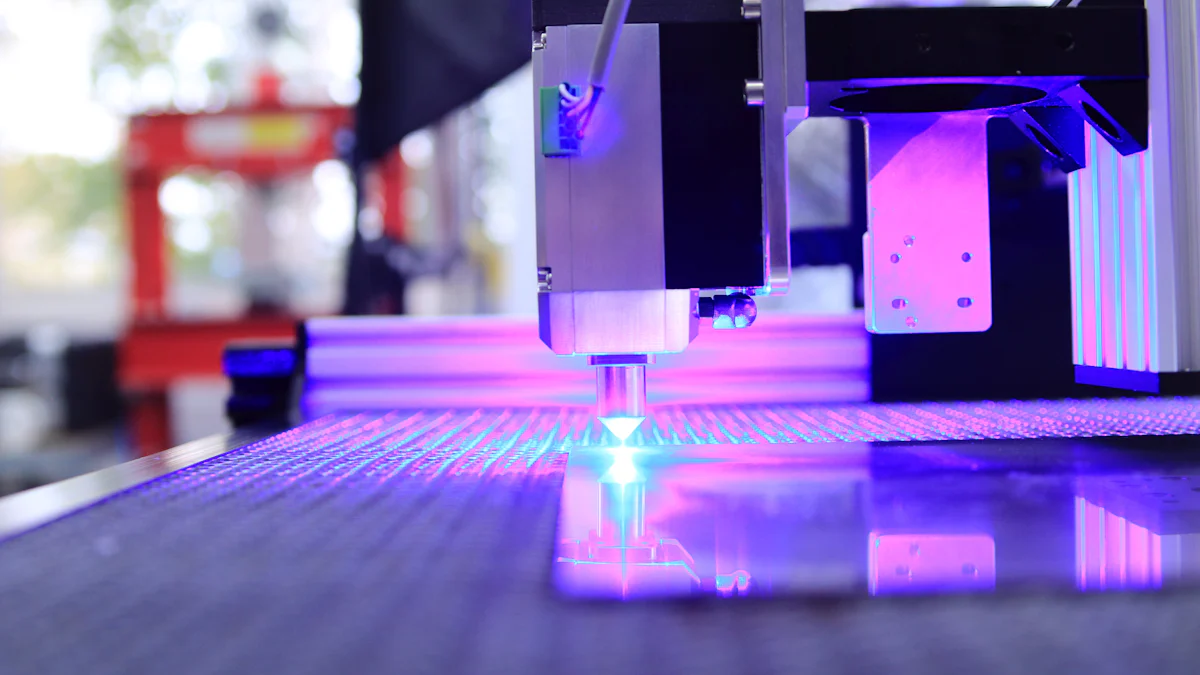
Energy-Efficient Machines
Reducing power consumption in manufacturing
Energy efficiency has become a cornerstone of modern manufacturing practices. Crystal cutting machine manufacturers now design equipment that consumes less power without compromising performance. Advanced technologies, such as variable frequency drives and energy-efficient motors, optimize energy usage during operations. These innovations not only lower electricity costs but also reduce the carbon footprint of manufacturing facilities. By prioritizing energy conservation, companies align with global sustainability goals while maintaining operational efficiency.
Adoption of renewable energy sources
The adoption of renewable energy sources is transforming the manufacturing landscape. Many facilities now integrate solar panels, wind turbines, and other renewable systems to power their operations. This shift reduces dependency on fossil fuels and supports long-term sustainability. For example, manufacturers in regions with abundant sunlight have installed photovoltaic systems to generate clean energy for their crystal cutting processes. These efforts demonstrate a commitment to eco-friendly practices and environmental stewardship.
Waste Reduction Technologies
Recycling crystal waste materials
Recycling plays a vital role in minimizing waste in the crystal cutting machine industry. Companies like Crystal Clean lead the way by promoting sustainable operations. They help manufacturers identify areas for improvement, such as reusing and re-refining materials. Their waste-to-energy processes convert discarded materials into usable energy, keeping waste out of landfills. These initiatives ensure that valuable resources remain within the supply chain, contributing to a circular economy.
Minimizing environmental impact
Manufacturers employ innovative techniques to reduce the environmental impact of their operations. Advanced filtration systems capture and treat waste byproducts, preventing harmful substances from entering ecosystems. Additionally, precision cutting technologies minimize material loss, ensuring that raw materials are used efficiently. These practices reflect the industry’s dedication to protecting the environment while maintaining high manufacturing standards.
Green Manufacturing Practices
Use of sustainable materials
The use of sustainable materials has gained traction in the crystal cutting machine industry. Manufacturers now source eco-friendly materials, such as recycled metals and biodegradable components, for their equipment. This approach reduces the environmental impact of production and supports the global push for greener manufacturing solutions. By adopting sustainable materials, companies enhance their reputation and appeal to environmentally conscious consumers.
Compliance with environmental regulations
Strict compliance with environmental regulations ensures that manufacturing processes meet global standards. Governments worldwide enforce policies that promote sustainability, such as limiting emissions and managing waste responsibly. Manufacturers adhere to these regulations by implementing green practices and investing in eco-friendly technologies. This compliance not only avoids legal penalties but also fosters trust among stakeholders and customers.
Crystal Cutting Machines Key Players
- Applied Materials
- Meyer Burger
- Shenyang Hanwei Machinery Manufacturing Co., Ltd.
- Nitto Denko Corporation
- Accretech
- Besi
- DISCO Corporation
- Komatsu NTC Ltd.
- Revasum
- Suzhou Delphi Laser Co., Ltd.
- Takatori Corporation
- Wuxi Lead Intelligent Equipment Co., Ltd.
- Yingkou Jinchen Machinery Co., Ltd.
- Zhejiang Jingsheng Mechanical & Electrical Co., Ltd.
Key Competitors
The market features a mix of established players and new entrants. Established companies typically lead in terms of brand recognition and reliability, while newer companies often compete by offering advanced features and competitive pricing. Innovation in cutting technology and customer service are crucial differentiators.
Competitive Strategies
To stay ahead, companies focus on technological upgrades such as integration of CNC (Computer Numerical Control) systems, automation, and AI-driven precision. Offering customized solutions, improving after-sales support, and maintaining a strong digital presence are key strategies for gaining market share in this sector.
Future Outlook for the Crystal Cutting Machine Market
Opportunities for Growth
Expansion into emerging markets
Emerging markets present significant opportunities for the crystal cutting machine industry. Latin America and the Middle East & Africa are beginning to recognize their potential in crystal growth applications. Investments in research and development are increasing in these regions, driven by industrialization and the rising demand for advanced manufacturing technologies. The establishment of academic institutions focusing on material science further accelerates interest in crystal cutting technologies. These developments create a fertile ground for market growth, offering manufacturers a chance to expand their global footprint.
Development of multi-functional machines
The demand for multi-functional machines is rising as industries seek versatile solutions to streamline operations. Manufacturers are developing machines capable of handling diverse materials and applications, from electronics to jewelry. These innovations align with smart manufacturing practices, enabling companies to optimize production processes. Multi-functional machines reduce the need for multiple devices, lowering costs and improving efficiency. This trend highlights the industry’s commitment to addressing evolving customer needs while embracing emerging technologies.
Potential Risks
Economic uncertainties and supply chain disruptions
Economic fluctuations and supply chain disruptions pose significant risks to the crystal cutting machine market. Global events, such as trade conflicts or pandemics, can impact raw material availability and production timelines. Manufacturers must adopt resilient strategies, such as diversifying suppliers and leveraging local resources, to mitigate these challenges. Proactive planning ensures stability and minimizes the impact of external factors on market growth.
Technological obsolescence and competition
Rapid advancements in technology trends create a risk of obsolescence for existing machines. Competitors continuously introduce innovative solutions, raising the bar for performance and efficiency. Manufacturers must invest in research and development to stay ahead of the curve. By adopting emerging technologies, they can maintain their competitive edge and meet the demands of a dynamic market.
Predictions for 2033
Increased adoption of AI-driven solutions
By 2033, the adoption of AI-driven solutions will likely dominate the crystal cutting machine industry. AI will enhance precision, automate processes, and enable predictive maintenance, reducing downtime and operational costs. These advancements will support smart manufacturing initiatives, ensuring consistent quality and efficiency across industries.
Greater focus on sustainability and innovation
Sustainability will remain a key priority for manufacturers. Companies will adopt eco-friendly practices, such as energy-efficient machines and waste reduction technologies, to align with global environmental goals. Innovation will drive the development of cutting-edge solutions, ensuring the industry continues to evolve and meet future challenges.
Overview
The global crystal cutting machine market in 2025 is characterized by technological advancements, sustainability initiatives, and expanding applications across industries. Innovations like AI integration and quantum computing are enhancing precision and efficiency, while energy-efficient machines and waste reduction technologies support environmental goals. The demand is driven by growing needs in electronics, jewelry, and medical sectors. Stakeholders must adapt to emerging trends and market dynamics, embracing innovation to position the industry for significant growth in the future.
Report Metric | Details |
---|---|
Report Name | Global Crystal Cutting Machine Market Report |
Base Year | 2024 |
Segment by Type | · Manual Crystal Cutting Machines
· Semi-automatic Crystal Cutting Machines · Fully automated Crystal Cutting Machines |
Segment by Application | · Electronics and Semiconductors
· Jewelry and Gemstones · Medical Devices and Optics |
Geographies Covered | · North America (United States, Canada)
· Europe (Germany, France, UK, Italy, Russia) · Asia-Pacific (China, Japan, South Korea, Taiwan) · Southeast Asia (India) · Latin America (Mexico, Brazil) |
Forecast units | USD million in value |
Report coverage | Revenue and volume forecast, company share, competitive landscape, growth factors and trends |
FAQ
What industries benefit the most from crystal cutting machines?
Electronics, semiconductors, jewelry, and medical devices benefit significantly. These industries rely on precise cutting technologies to produce high-quality components like silicon wafers, gemstones, and optical lenses. Advanced machines enhance efficiency and reduce material waste, meeting the stringent demands of these sectors.
How does AI improve crystal cutting machine performance?
AI enhances precision by analyzing material properties and adjusting cutting parameters in real time. It also enables predictive maintenance, reducing downtime and operational costs. These advancements ensure consistent quality and efficiency, supporting industries with high accuracy requirements.
Are crystal cutting machines environmentally friendly?
Modern machines incorporate energy-efficient technologies and waste reduction systems. Manufacturers adopt renewable energy sources and sustainable materials to minimize environmental impact. These eco-friendly innovations align with global sustainability goals and reduce the carbon footprint of manufacturing processes.
What challenges do manufacturers face in adopting advanced machines?
High initial investment costs and a shortage of skilled operators pose significant challenges. Training programs and workforce development initiatives are essential to address these issues. Manufacturers must also balance technological advancements with affordability to ensure widespread adoption.
Which regions dominate the crystal cutting machine market?
Asia-Pacific leads due to its robust manufacturing hubs and cost-effective labor. North America and Europe focus on innovation and sustainability, while emerging markets in Latin America and the Middle East show increasing adoption driven by industrialization and demand for advanced technologies.
Global Crystal Cutting Machine Market Report – Table of Contents
1 Market Study Overview
2 Basic Product Information
3 Market Analysis
4 Crystal Cutting Machine Related Market Analysis
5 Global Trend Summary
6 Competition by Manufacturer
7 Analysis of Key Players
8 Global Crystal Cutting Machine Revenue, Sales Categorized by Regions
9 North America Crystal Cutting Machine Market Size Categorized by Countries
10 Europe Crystal Cutting Machine Market Size Categorized by Countries
11 Asia-pacific Crystal Cutting Machine Market Size Categorized by Countries
12 South America Crystal Cutting Machine Market Size Categorized by Countries
13 Middle East and Africa Crystal Cutting Machine Market Size Categorized by Countries
14 Global Crystal Cutting Machine Industry Segment Analysis
15 Global Crystal Cutting Machine Market Forecast
16 Research Findings and Conclusion
17 Appendix