$232.51 Million Friction Stir Welding Equipment Market Heats Up in 2025: U.S., China, and Germany Drive Demand
Discover the $232.51M global Friction Stir Welding Equipment Market forecast for 2025, with insights on the U.S., China, and Germany.
- Last Updated:
Friction Stir Welding Equipment Market Q1 and Q2 2025 Forecast
The Friction Stir Welding Equipment market is estimated to reach $232.51 million in 2025, with a CAGR of 6.8% from 2025 to 2033. In Q1 2025, the market is expected to generate approximately $58 million, driven by demand from the automotive and aerospace industries in the U.S., China, and Germany.
Factors Driving Growth
- Demand for lightweight materials in automotive manufacturing
- Adoption of advanced welding technologies in aerospace applications
- Focus on automotive innovation and defense technology in the U.S. and Germany
- Expansion of aerospace and automotive production capabilities in China
Friction stir welding (FSW) is a solid-state joining process used in lightweight materials and is widely adopted in automotive manufacturing and aerospace applications where traditional welding methods are inefficient. With the increasing demand for high-performance materials in these industries, FSW equipment is poised to see strong growth.
Market Projections
By Q2 2025, the market is projected to reach $60 million, with China expanding its aerospace and automotive production capabilities, driving demand for advanced welding technologies.
The U.S. and Germany will also continue to contribute significantly, given their focus on automotive innovation and defense technology. The trend towards lighter, stronger materials in manufacturing will be a key growth factor.
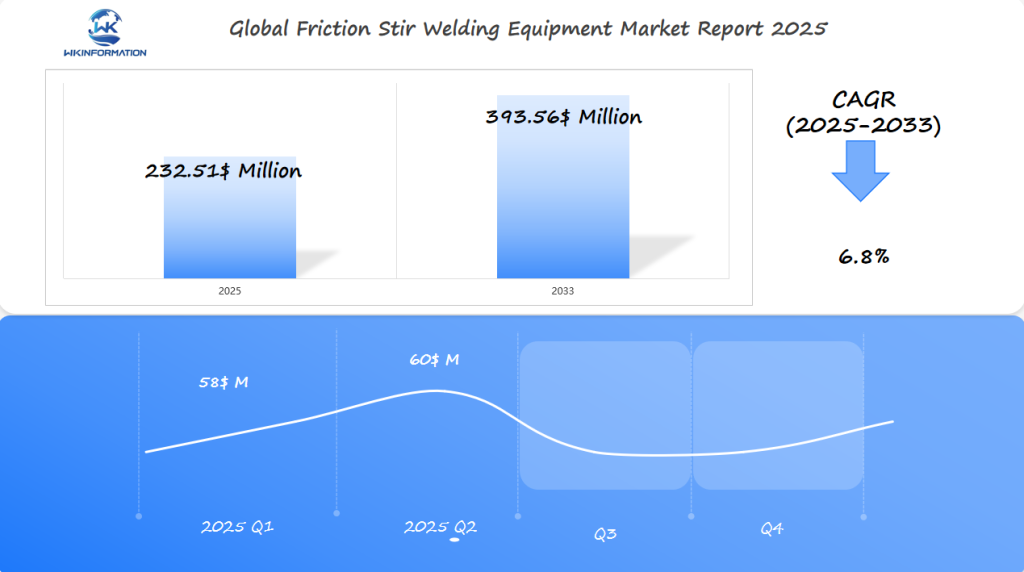
Understanding the Supply Chains in Friction Stir Welding
The world of friction stir welding relies on a complex network of suppliers and users. To grasp its functioning, we can break it down into two main parts: the upstream and downstream industry chains.
The Upstream Supply Chain
The upstream welding supply chains begin with raw materials such as aluminum alloys and copper-based components. Key players in this segment include:
- Metal producers: Companies like Alcoa and Novelis that produce aluminum and other metals.
- Component fabricators: Manufacturers who use these metals to create specific parts or components for welding equipment.
These component fabricators play a crucial role in supplying materials to makers of welding equipment.
The Downstream Supply Chain
On the downstream side, various entities work together to connect manufacturers with end-users. This chain consists of:
- Equipment sellers: Distributors such as Miller Welds and Lincoln Electric who sell welding machines and tools.
- Final industry buyers: Industries that directly use these machines for their operations, such as aerospace companies building satellites or car manufacturers producing electric vehicles.
The collaboration between these layers is vital for ensuring efficient delivery and quality control throughout the supply chain.
Why Understanding These Chains Matters
By understanding these connections, stakeholders can:
- Predict market shifts
- Identify new opportunities
- Optimize costs
- Foster innovation
As industries increasingly adopt environmentally friendly practices, suppliers are responding by offering recycled aluminum to meet sustainability goals. This shift has implications for both ends of the chain, making the entire system more efficient and reinforcing the importance of collaboration within the friction stir welding ecosystem.
Key Trends Driving the Friction Stir Welding Equipment Market: Aerospace and Automotive Expansion
New Aerospace Automotive Welding Trends are boosting demand for friction stir welding (FSW) tech. It’s favored for joining lightweight materials without losing strength. This change is altering how both industries make things.
Aerospace Applications
Aerospace companies use FSW to weld aluminum alloys for aircraft parts. This reduces weight and saves fuel.
Automotive Applications
Automotive firms use FSW for electric vehicle (EV) battery enclosures. It ensures they are leak-proof and resistant to corrosion.
Cost Efficiency through Automation
Adding automation makes FSW cheaper for making lots of parts.
Industry | Material Focus | Key Application |
Aerospace | Aluminum alloys | Jet engine parts, fuselage structures |
Automotive | High-strength steels | EV battery packs, lightweight body panels |
Big names like Boeing and Tesla are quick to adopt FSW. They use it to meet their green goals. The move towards electric and light vehicles keeps FSW key for future making.
Challenges in Friction Stir Welding Equipment Manufacturing and Adoption
Creating and using friction stir welding equipment comes with big Welding Equipment Manufacturing Challenges. Making tools that work well is hard because of material and heat issues. Companies like Amada Miyachi and Fronius work hard to solve these problems but it costs a lot.
Key Challenges in Friction Stir Welding Equipment Manufacturing
Here are some of the main challenges faced in the manufacturing of friction stir welding equipment:
- High upfront costs: Small manufacturers may find it difficult to upgrade their equipment due to the high initial costs involved.
- Operator training: Advanced systems require specialized training for operators, which can be a barrier to adoption.
- Regulatory confusion: Global standards for welding may vary, leading to confusion in regulatory compliance.
Ensuring quality is also a big task. Small changes in materials can affect weld strength, needing careful setup. Companies like Lincoln Electric now make modular designs to fit different needs.
Even with these challenges, new tech like automation and AI is helping. Companies like Trumpf are making systems that check quality as it happens. As more people need this technology, solving these Welding Equipment Manufacturing Challenges will lead to better, safer ways to make things.
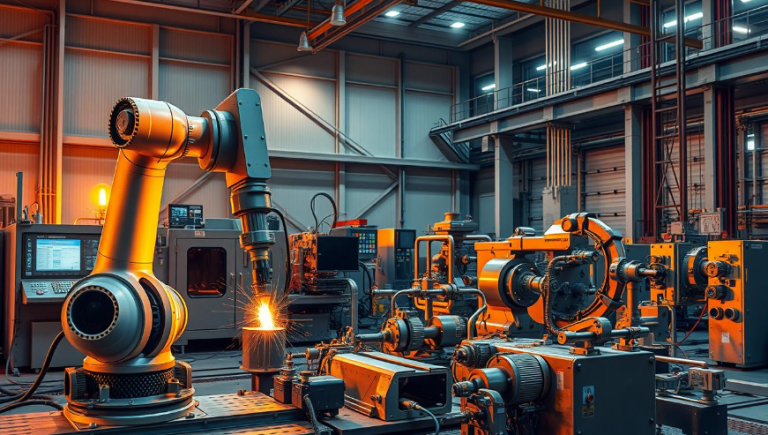
Geopolitical Influence on the Friction Stir Welding Equipment Market
Geopolitical factors play a big role in the growth of the welding equipment market. Trade policies, sanctions, and partnerships between countries affect costs, supply chains, and demand.
- Trade wars between big countries slow down deliveries and increase prices.
- Regional alliances, like the EU’s Green Deal, increase demand for green welding tech.
- Sanctions on tech exports limit access to advanced machines in developing countries.
U.S. sanctions on China have slowed down joint ventures in car welding projects. Germany’s trade with the EU ensures steady demand for precise tools. This geopolitical impact also drives innovation as countries invest in local manufacturing to reduce reliance on others.
Country | Key Policy | Market Effect |
U.S. | Defense spending | Rises aerospace welding orders |
China | Belt and Road Initiative | Boosts infrastructure welding demand |
Germany | EU climate laws | Increases green welding tech adoption |
Companies need to keep an eye on trade agreements and geopolitical changes. They must balance global and local strategies to navigate this changing market landscape.
Friction Stir Welding Equipment Market by Type: Fixed, Portable, and Robotic Systems
Manufacturers have three main options: Fixed, Portable, and Robotic Welding Systems. Each type has its own benefits for different industries.
Fixed Welding Systems | High precision, suited for mass production | High installation costs, limited mobility | Aerospace, automotive assembly lines |
Portable Welding Systems | Easy transportation, cost-effective for small projects | Lower output capacity | Construction sites, field repairs |
Robotic Wielding Systems | Automated processes, consistent quality | High upfront investment | Automotive, shipbuilding, high-volume production |
Big names like Lincoln Electric and Fronius lead in Fixed systems. Meanwhile, Miller Welding offers portable solutions for field work. FANUC and ABB are top in robotic welding, used in places like Tesla’s car factory.
Companies pick based on budget, space, and project size. Portable systems are good for short-term jobs. Robotic systems are best for repetitive tasks. The right choice saves money and boosts efficiency.
Applications of Friction Stir Welding Equipment in Automotive, Aerospace, and Shipbuilding
Friction stir welding (FSW) is revolutionizing manufacturing processes across various industries. In the automotive sector, it’s instrumental in producing lighter car frames and specialized enclosures for electric vehicle batteries. The aerospace industry benefits from FSW as well, using it to meticulously join fuel tanks and engine components.
When it comes to shipbuilding, FSW is the technique of choice for welding together the hulls and other parts of large vessels. These welding applications not only reduce costs but also enhance the longevity of the products.
Automotive | Car frames, body panels | Stronger joints, reduced material waste |
Aerospace | Jet engine components, satellite structures | Heat resistance, leak-proof seals |
Shipbuilding | Marine hulls, propulsion systems | Corrosion resistance, faster production |
Prominent companies like Tesla and Boeing rely on FSW for ensuring safety in their products. In shipbuilding, firms such as Damen Shipyards utilize this technology for large-scale projects. The implementation of FSW significantly minimizes errors and accelerates production across all three sectors.
As the demand for these products continues to rise, FSW is being applied to new materials such as aluminum alloys. Its importance in these industries underscores its vital role in modern manufacturing.
Global Insights into the Friction Stir Welding Equipment Market
Global Welding Market Insights show a market influenced by local needs and new tech. In North America, aerospace is key, while Asia-Pacific sees a surge in manufacturing. Each area brings its own spark to innovation.
- North America: Leading in aerospace and defense applications, driven by U.S. tech advancements.
- Asia-Pacific: Rapid adoption in automotive manufacturing, fueled by cost-efficient solutions.
- Europe: Prioritizes sustainability, integrating eco-friendly welding practices.
In Africa and the Middle East, new economies are investing in big projects. This boosts demand for easy-to-use systems. Europe, meanwhile, focuses on green welding, pushing for eco-friendly tools.
Fixed systems are common in big industrial areas. But, portable systems are gaining ground in remote construction sites.
Global Welding Market Insights also show how partnerships help in equipment exports. For example, U.S. and Asian firms team up. Automation is on the rise, making robotic systems essential in factories worldwide.
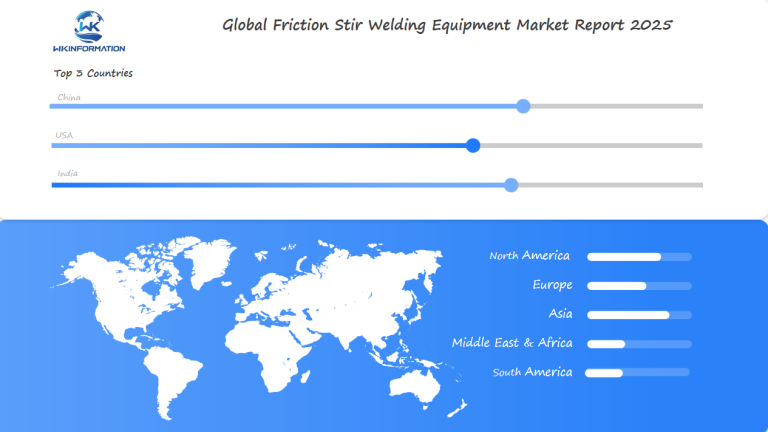
The U.S.’s Leadership in Advanced Welding Technologies for Aerospace and Defense
The U.S. is leading the way in Advanced Welding Technologies, making significant advancements in the aerospace and defense industries. Major companies such as Boeing and Lockheed Martin are utilizing friction stir welding to manufacture aircraft and spacecraft that are both lighter and stronger.
This innovative approach not only reduces costs but also enhances the durability of military jets and satellites.
Collaborations for Advancements
NASA and Sandia National Laboratories are partnering with private companies to push the boundaries of materials science. Their primary focus is on welding heat-resistant alloys for hypersonic vehicles and next-generation rockets. To ensure the competitiveness of U.S. factories, government grants are being allocated to support research in automation.
Key Developments
Here are some notable developments in advanced welding technologies:
- Lockheed Martin employs robotic welding for F-35 fighter components, resulting in a 30% reduction in production time.
- Boeing’s collaborative programs with MIT have led to the creation of lightweight joints for space stations, improving safety measures.
- Sandia’s report from 2023 highlights that $250 million in federal grants have been allocated for research and development of welding technology since 2020.
Supporting Defense Contracts
The U.S. Advanced Welding Technologies also play a crucial role in supporting defense contracts. Armored vehicles and missile systems require seamless welds to ensure their strength and integrity.
Public-private laboratories such as the Southwest Research Institute are at the forefront of developing techniques for titanium and aluminum composites, which are essential for modern military technology.
Continuous Innovation
As global competition intensifies, U.S. innovation remains unparalleled. These advanced technologies provide the nation with a competitive advantage in high-stakes industries. By consistently investing in research and development, the U.S. can maintain its position as a global leader for many years ahead.
China’s Rapid Growth in Friction Stir Welding Equipment for Automotive Manufacturing
China is leading the way in car production worldwide. Big names like Changan Automobile and Geely are adopting new welding technologies such as friction stir welding. This innovation makes manufacturing cars cheaper and faster, especially for electric and hybrid models.
China Automotive Welding Growth
- Government subsidies for automation projects
- Partnerships with tech firms for AI-driven welding robots
- Expansion of joint ventures with European equipment suppliers
Car parts makers are using robots to weld faster. This cuts down production time by 30%. It also helps them send lightweight car parts to places like the EU and Southeast Asia. Thanks to “Made in China 2025,” factories are getting smarter, leading to more growth in welding.
Germany’s Expertise in High-Precision Welding Equipment for Industrial Applications
Germany is known for its High-Precision Welding Equipment. Leaders like Trumpf and Siemens offer systems that are fast and accurate. These machines are perfect for making flawless joints in industries like cars and planes.
Innovation Focused on Durability and Performance
German innovation is all about making things last and work better. Their equipment has real-time monitoring, so every weld is up to standard. For instance, Trumpf’s TruDUR line cuts down on mistakes by 90% compared to old methods. This makes Germany High-Precision Welding Equipment a favorite worldwide.
Key Features of Germany’s High-Precision Welding Equipment
- ISO 9001-certified quality control
- Adaptability for aluminum and composite materials
- Low maintenance costs over long-term use
Feature | Germany’s Approach | Industry Impact |
Precision | ±0.1mm tolerance standards | Reduced post-weld adjustments |
Automation | AI-driven calibration systems | Cuts labor hours by 40% |
Material Compatibility | Customizable for titanium and carbon steel | Expands application possibilities |
As the world looks for ways to work better, these systems offer precision without giving up quality. Companies all over the world rely on Germany for their welding needs.
The Future of Friction Stir Welding Equipment: Automation and Smart Welding Systems
Future Smart Welding Automation is changing welding forever. Imagine machines that learn and adjust on their own. Smart sensors and predictive analytics will make this possible. They will help machines change settings based on the material and project needs.
- AI algorithms reduce human error by analyzing weld quality instantly.
- IoT-connected devices share data across factories, improving maintenance schedules.
- Robotic arms guided by machine learning handle complex automotive and aerospace parts with precision.
These new tools save money and reduce downtime. For instance, real-time defect detection stops problems before they start. Companies using these technologies can increase productivity by up to 40%, trials show. This tech also makes work safer by letting robots handle dangerous tasks.
Top equipment makers are adding these features to their products. Now, smart systems can find and fix problems themselves, cutting down on unexpected stops. As the need for lighter materials grows, automation ensures quality in cars and planes. This technology is not just a trend—it’s essential for staying ahead in tough manufacturing.
Competitive Landscape in the Friction Stir Welding Equipment Market
The friction stir welding equipment market is changing fast. Companies like TWI, ESAB, and Amada WELD TECH are leading the way. They focus on making things more automated and precise.
Key Players in the Market
Here are some of the key players in the friction stir welding equipment market:
- ETA Technology Pvt. Ltd. – India
- YAMAZAKI MAZAK Corporation – Japan
- FOOKE GmbH – Germany
- PaR Systems Inc. – United States
- Hitachi Power Solutions Co. Ltd. – Japan
- Nitto Seiki Co. Ltd. – Japan
- Grenzebach Group GmbH & Co. KG – Germany
- Bond Technologies Inc. – United States
- Beijing FSW Technology Co. Ltd. – China
- Nova-Tech Engineering – United States
Overall
Report Metric | Details |
---|---|
Report Name | Global Friction Stir Welding Equipment Market Report |
Base Year | 2024 |
Segment by Type |
· Fixed · Portable · Robotic Systems |
Segment by Application |
· Automotive · Aerospace · Shipbuilding |
Geographies Covered |
· North America (United States, Canada) · Europe (Germany, France, UK, Italy, Russia) · Asia-Pacific (China, Japan, South Korea, Taiwan) · Southeast Asia (India) · Latin America (Mexico, Brazil) |
Forecast units | USD million in value |
Report coverage | Revenue and volume forecast, company share, competitive landscape, growth factors and trends |
The friction stir welding equipment market continues to evolve rapidly across automotive, aerospace, and shipbuilding sectors. With increasing demand for lightweight materials and stronger joints, FSW technology remains at the forefront of modern manufacturing. The market shows promising growth potential, driven by technological advancements, automation integration, and expanding applications across industries.
As manufacturers focus on sustainability and efficiency, friction stir welding equipment will play an increasingly vital role in shaping the future of industrial welding processes. The continued innovation in this field, coupled with growing adoption across global markets, positions friction stir welding equipment as a crucial component in the future of manufacturing technology.
Global Friction Stir Welding Equipment Market Report (Can Read by Free sample) – Table of Contents Chapter 1: Friction Stir Welding Equipment Market Analysis Overview Competitive Forces Analysis (Porter’s Five Forces) Strategic Growth Assessment (Ansoff Matrix) Industry Value Chain Insights Regional Trends and Key Market Drivers Friction Stir Welding EquipmentMarket Segmentation Overview Chapter 2: Competitive Landscape Global Friction Stir Welding Equipment players and Regional Insights oKey Players and Market Share Analysis Sales Trends of Leading Companies oYear-on-Year Performance Insights Competitive Strategies and Market Positioning oKey Differentiators and Strategic Moves Chapter 3: Friction Stir Welding Equipment Market Segmentation Analysis Key Data and Visual Insights oTrends, Growth Rates, and Drivers Segment Dynamics and Insights oDetailed Market Analysis by Segment Chapter 4: Regional Market Performance Consumer Trends by Region oHistorical Data and Growth Forecasts Regional Growth Factors oEconomic, Demographic, and Technological Impacts Challenges and Opportunities in Key Regions Regional Trends and Market Shifts Key Cities and High-Demand Areas Chapter 5: Friction Stir Welding Equipment Emerging and Untapped Markets Growth Potential in Secondary Regions oTrends, Challenges, and Opportunities Chapter 6: Product and Application Segmentation Product Types and Innovation Trends Application-Based Market Insights Chapter 7: Friction Stir Welding Equipment Consumer Insights Demographics and Buying Behaviors oTarget Audience Profiles Chapter 8: Key Findings and Recommendations Summary ofFriction Stir Welding Equipment Market Insights Actionable Recommendations for Stakeholders
Chapter 1: Friction Stir Welding Equipment Market Analysis Overview
- Competitive Forces Analysis (Porter’s Five Forces)
- Strategic Growth Assessment (Ansoff Matrix)
- Industry Value Chain Insights
- Regional Trends and Key Market Drivers
- Friction Stir Welding EquipmentMarket Segmentation Overview
Chapter 2: Competitive Landscape
- Global Friction Stir Welding Equipmentplayers and Regional Insights
- Key Players and Market Share Analysis
- Sales Trends of Leading Companies
- Year-on-Year Performance Insights
- Competitive Strategies and Market Positioning
- Key Differentiators and Strategic Moves
Chapter 3: Friction Stir Welding Equipment Market Segmentation Analysis
- Key Data and Visual Insights
- Trends, Growth Rates, and Drivers
- Segment Dynamics and Insights
- Detailed Market Analysis by Segment
Chapter 4: Regional Market Performance
- Consumer Trends by Region
- Historical Data and Growth Forecasts
- Regional Growth Factors
- Economic, Demographic, and Technological Impacts
- Challenges and Opportunities in Key Regions
- Regional Trends and Market Shifts
- Key Cities and High-Demand Areas
Chapter 5: Friction Stir Welding Equipment Emerging and Untapped Markets
- Growth Potential in Secondary Regions
- Trends, Challenges, and Opportunities
Chapter 6: Product and Application Segmentation
- Product Types and Innovation Trends
- Application-Based Market Insights
Chapter 7: Friction Stir Welding Equipment Consumer Insights
- Demographics and Buying Behaviors
- Target Audience Profiles
Chapter 8: Key Findings and Recommendations
- Summary ofFriction Stir Welding EquipmentMarket Insights
- Actionable Recommendations for Stakeholders
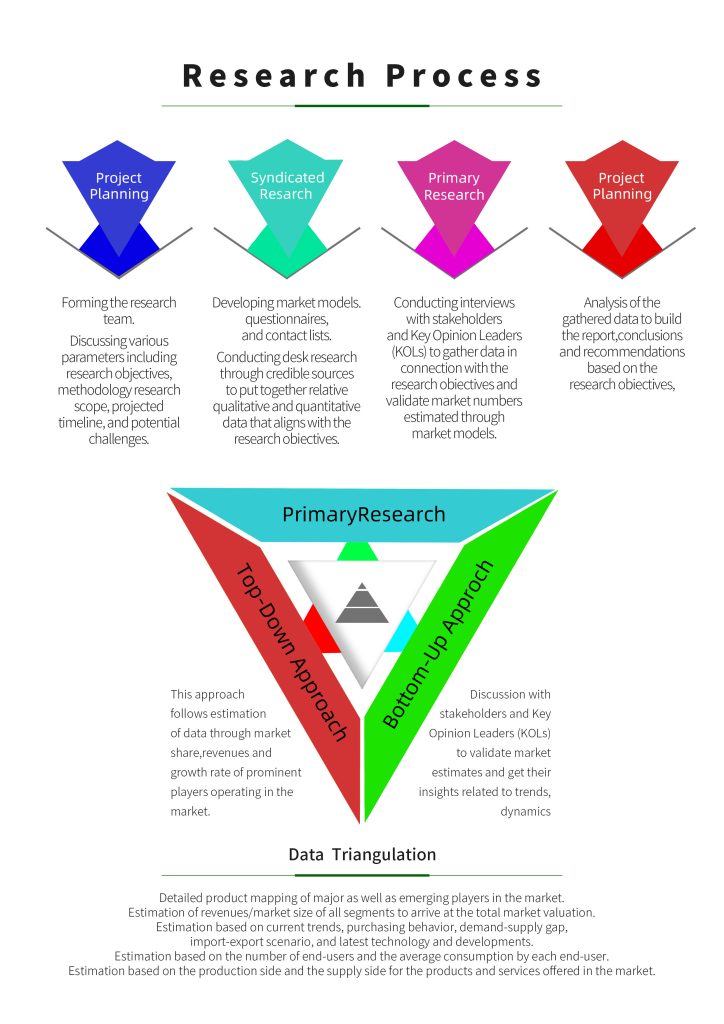
Access the study in MULTIPLEFORMATS
Didn’t find what you’re looking for?
TALK TO OUR ANALYST TEAM
Need something within your budget?
NO WORRIES! WE GOT YOU COVERED!
Call us on: +1-866-739-3133
Email: infor@wkinformation.com
What is friction stir welding equipment?
Friction stir welding equipment is a specialized tool used for joining metals together. It works by generating heat through friction caused by mechanical stirring. This process allows for the creation of strong welds without actually melting the metal being worked on.
Why is the friction stir welding market growing?
The market is growing because of high demand in car, plane, and ship making. People want efficient and strong manufacturing. New technology also helps more people use this equipment.
What are the main applications of friction stir welding?
Friction stir welding is primarily used in various industries for specific purposes:
- Automotive Industry: It is mainly used in car manufacturing for joining lighter parts, which helps in reducing the overall weight of vehicles and improving fuel efficiency.
- Aerospace Industry: In the aviation sector, friction stir welding is employed to join components of aircraft structures, providing enhanced strength and structural integrity.
- Shipbuilding Industry: It finds application in shipbuilding for joining thick sections of metal, ensuring durability and resistance to harsh marine conditions.
The advantages of friction stir welding, such as improved production efficiency and stronger joints, make it a preferred choice in these industries.
How does geopolitics influence the friction stir welding equipment market?
Politics, including trade rules, have a significant impact on the market. Changes in trade can disrupt supply chains and market access, affecting both manufacturers and buyers.
What are the types of friction stir welding systems available?
There are fixed systems, portable machines, robotic ones, and options from companies like Bugo. Each has its own benefits for different needs, like being mobile or precise.
What challenges do manufacturers face in this industry?
Manufacturers face technology challenges, high costs, and strict regulations. These issues can slow down production and impact the quality of products.
Who are the key players in the global friction stir welding equipment market?
Leading companies such as Fronius, ESAB, and KUKA are at the forefront of the industry. They are advancing the technology, establishing benchmarks through their efforts, and fostering expansion.
What role does automation play in the future of friction stir welding?
Automation will change the market by adding smart systems and AI. This will make welding better and more efficient. It’s expected to boost productivity a lot. For instance, the integration of advanced technologies, as shown in this image, illustrates how automation can enhance the friction stir welding process.